Essential Considerations When Installing Warehouse Roller Shutters
- Amelia Varley
- Mar 5
- 4 min read
Have you found yourself wondering if a simple door upgrade could significantly improve your warehouse operations? Are you curious about how a well-crafted roller shutter plan can boost both security and efficiency in your facility? If so, you’re in the right place. In this blog post, we’ll explore the key factors to consider when choosing and installing warehouse roller shutters in Australia.

Roller shutters installation isn’t merely about picking a door and attaching it to your building. It involves mapping out a rolling shutter plan, meeting building regulations, and ensuring a suitable design for your operational needs. Whether you’re taking on a new warehouse build or upgrading an existing space, knowing these vital steps can help you avoid hiccups down the track.
By reading on, you’ll discover what a shutter door plan looks like, why a rolling shutter plan matters so much, and how to install industrial roller shutter door systems safely. We’ll also cover maintenance tips, safety guidelines, and frequently asked questions. Let’s jump straight in and demystify the entire process, so you can move forward with confidence and peace of mind.
Assessing Your Warehouse Requirements
Before finalising any roller shutter installations, it’s vital to think about what your warehouse really needs. Every building has its own dimensions, operational flow, and safety standards, so there’s no one-size-fits-all shutter door plan. The goal is to find a system that lines up with the space, traffic levels, and compliance rules in your region.
Determining Space Constraints and Traffic Flow
First, think about where vehicles and staff regularly move around. If your facility sees a constant flow of trucks, you’ll need a rolling shutter plan that accommodates large vehicles. This means installing roller shutter doors with enough clearance for both height and width. Similarly, if you handle stock frequently, you might want more than one shutter door installation to manage heavy traffic, reduce loading times, and streamline operations.
Additionally, consider how people and forklifts navigate the warehouse. A cramped doorway can disrupt productivity. On top of that, you need to plan for any overhead piping, lighting fixtures, or structural beams that could interfere with the door’s movement. By mapping out these details in advance, you can avoid costly surprises and keep your roller shutter plan on track.
Compliance with Australian Building Codes and Regulations
When you’re drawing up your shutter door plan, remember to check local requirements. Australian building codes often specify minimum clearances, emergency exit spacing, and other regulations that apply to industrial warehouse roller shutter door installations. Overlooking these rules isn’t just risky—it could mean fines, shut-down orders, or the need for expensive rework.
Thankfully, most building authorities provide guides on minimum standards for rolling shutter in plan requirements. It’s also wise to consult a specialist or structural engineer if you’re unsure about compliance. By doing so, you’ll confirm that your shutter door installation meets all necessary safety expectations, saving you headaches and potential legal complications later.
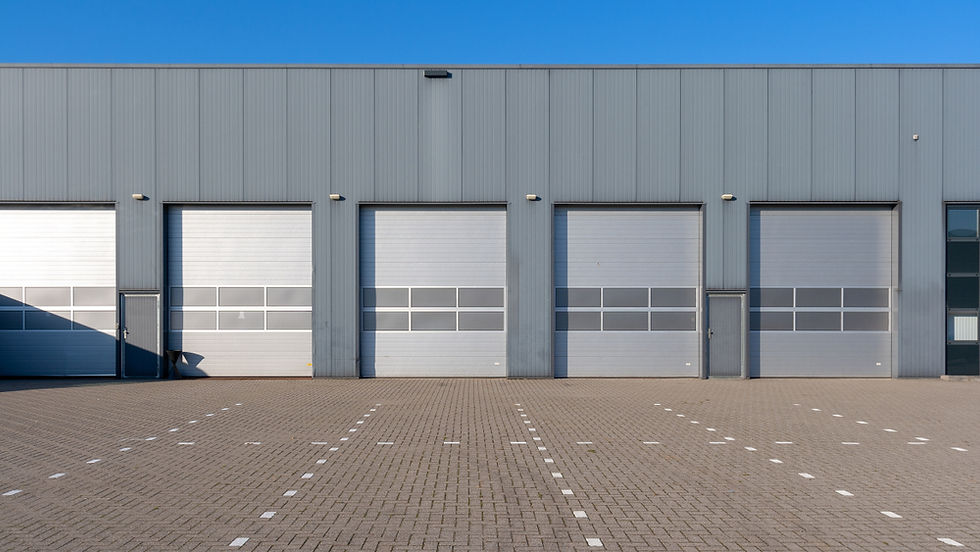
Choosing the Right Roller Shutters for Your Facility
A roller shutter plan that suits a small retail space might not be robust enough for a busy warehouse. Each business faces unique challenges, from daily temperature changes to heavy machinery use. In this section, we’ll explore how to make a well-informed choice.
Material Selection and Durability
Warehouse Roller shutters come in an array of materials, such as steel, aluminium, or polycarbonate. Steel shutters usually provide the highest level of security, making them popular in industrial settings. They can handle harsh weather and daily wear without warping or bending, plus they deter unauthorised entry better than most alternatives. Aluminium is lighter and resistant to rust, which is helpful in locations with high moisture or salty air.
When finalising your rolling shutter plan, remember that material choice also affects cost. Overall, sturdier materials often mean a bigger initial investment, but they pay off in the long run by lasting longer and requiring less frequent maintenance. It’s crucial to strike a balance between durability and budget to get the best possible return on your purchase.
Manual vs. Automated Systems
Should you go for manual or automated controls? This decision depends on staff availability, the volume of traffic, and the size of your shutters. Manually operated doors might be more affordable upfront, but they can be cumbersome for larger shutters or high-traffic areas. Conversely, automated warehouse roller shutters installation can streamline operations, especially if you have multiple entrances or a busy loading dock.
How to Install Industrial Roller Shutter Door: Step-by-Step
Installing roller shutter doors can be straightforward if you have the right tools and follow the correct instructions. This section offers a simple step-by-step guide, but remember that some installations may call for advice from seasoned professionals.
Tools and Equipment Checklist
Gather everything before you begin. You’ll likely need:
A measuring tape and level
Drill with appropriate bits
Anchors and screws
Ladder or scaffolding (depending on door height)
Safety gloves, goggles, and a helmet
The roller shutter kit itself, including tracks and brackets
Being well-prepared reduces downtime and prevents last-minute dashes to the hardware store. You’ll also need a stable power supply for your tools. Double-check your items ahead of time so that the day of the install runs as smoothly as possible.
Conclusion
When done correctly, a roller shutter installation can be a real game-changer for warehouse operations. From selecting the right materials to mapping out a rolling shutter in plan, each stage influences security, efficiency, and overall durability. Taking the time to plan thoroughly reduces the likelihood of issues, ensuring a smoother experience for both workers and supervisors.
Comments